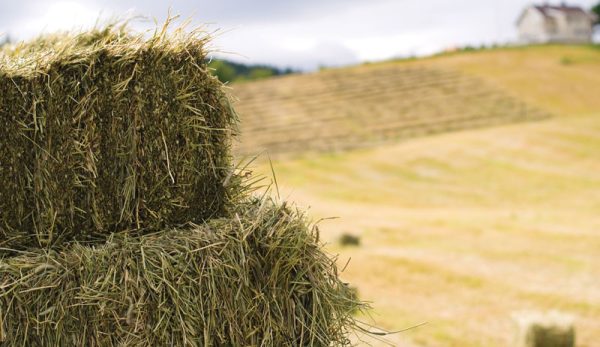
It all started when my girlfriend, Lori, bought a farm. (I have never seen a Hobby Farms article begin this way, and the reason could be that it isn’t nearly as entertaining as I find it. But I felt it had to be done!) The farm we started with three years ago sits barely within the city limits of a small Arkansas college town.
It’s comprised of 40 acres, 20 of which are unimproved pasture intermittently surrounded by decaying fencing. The other 20 consist largely of structures, lawn, old-growth hardwood groves and Chinese privet hedge thickets, interspersed with impenetrable saw briars, rocks and brambles.
It’s home to approximately 7.23 billion ticks and chiggers, four goats, four farm dogs and 43 chickens (give or take).
Hay Pasture Problems
Lori purchased the farm in April 2019 on the eve of summer. So one of the very first concerns was what to do with the pasture.
A lawn-care professional friend recommended we partner with another farmer to bale the hay in the fields. Although prices may vary by region, there are several different, fairly consistent arrangements for partnering with someone who owns the equipment to bale the fields.
As the landowner, you may simply sell all your bales to your farming partner. Most farmers raising livestock who bale other people’s land raise cattle and will produce round bales. Round bales can weigh 1,000 to 2,000 pounds each, depending on moisture content and size. They require a tractor to move them.
Here, a farmer will pay around $5 per bale to cut, rake, bale and carry off your hay. Our 20 acres yields around 60 round bales. This option would mean about $300 per cutting, total.
Other options include some form of “on the halves,” wherein the person with the equipment cuts, rakes, bales and hauls off 2⁄3 of the bales. They leave the other third laying in the field for the landowner.
This option could be advantageous to landowners with livestock of their own. Even if we had purchased a small herd of livestock, we wouldn’t have had it long enough to enjoy this arrangement due to the poor condition of the fence.
Another option that our particular partner was interested in involved square bales. Each round bale contains roughly the equivalent of 15 square bales of hay. But whereas round bales require a tractor to move and sell for around $30 each, square bales only weigh around 50 pounds each and sell for $5 each.
This means the equivalent sale price of the square bales made from the amount of hay in each $30 round bale is $75.
Our partner agreed to cut, rake and bale if my girlfriend would store and market the bales, splitting proceeds 50/50. We were able to cut hay twice that first summer and put up around 1,000 bales each time, making our split a ballpark $2,500 each time.
Our haymaking partner owns a grass-fed beef farm, works full-time at a tractor dealership, part-time in military guard and reserves, and about 17 other jobs. So he often needed help in his various haymaking activities in the farmland surrounding our town. I worked for him on an hourly basis and learned to use his tractor and other equipment, making hay on other properties he had arranged to cut.
When I saw how easy, therapeutic and even fun it was to work the fields, I began to explore purchasing my own equipment. The first advisors were friends who worked at tractor dealerships, who assured us $80,000 to $100,000 of equipment was necessary.
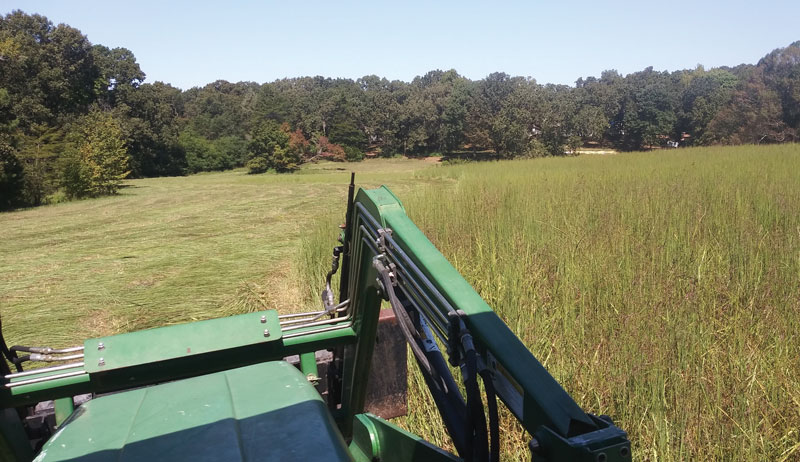
Do I Need a Tractor to Make Hay?
Some of the most vivid and entertaining discussions my girlfriend and I had were over whether a tractor was a necessity or the biggest waste of money ever hoisted upon small farmers.
She saw rusty hulks littering fields throughout the South as proof positive that the best option (if a tractor was indeed even necessary) was some sort of tractor ownership-sharing plan. I argued, never having encountered anyone else interested in sharing, that the point was a machine you could use whenever you needed it, regardless when some other owner needed it.
I was new enough to haymaking that I felt I should ask someone in the know what exactly I’d need if I was going to take over the hay operation. Our hay partner assured me that if I wanted to make hay, the implements needed would require 60 to 70 horsepower. He used a 90-plus horsepower machine with enclosed cab, air conditioning, radio, etc. worth around $75,000, even though it was 10 years old.
To win the tractor argument, I needed a tractor and implements that would be paid for in about one or two cuttings, so $5,000 to $10,000 altogether. I watched Facebook Marketplace, Craigslist, auctions and local mom-and-pop tractor lots in vain.
In the end, I gave up on cutting my own hay. But I did find a reasonably-priced used tractor for sale that I decided I needed for other projects such as moving earth and discing.
Read more: Loose hay? Here’s 4 things you can do with it.
Square Market
As it turns out, the number of people starting small farms is increasing. Small farms lend themselves to sheep, goats and small cattle herds. These are prime customers for square bales of hay.
Additionally, what we hear from our customers is that haymakers are moving from the labor-intensive square bales to equipment-intensive round bales. This makes square bales more difficult to find.
This opens up a nice niche market for small farms with grass pastures to cut and bale square bales for sale to other small farmers.
Marketing was probably the easiest part of the hay business as far as I was concerned. Why? Well, Lori did it all.
She joined several farm-related Facebook groups and would simply post when we had hay. She often gave a discount if bales were purchased straight from the field, saving us moving them to the barn. This accounted for about 250 bales each cutting.
We always sold out of hay before our next cutting.
New versus Used
The simplest hay operation requires a tractor, a cutter, a rake and a baler. You’ll find endless information online to compare the various options for each implement, and all kinds of opinions about matching their size with the tractor pulling them so I won’t go into depth here about those details.
I’ll simply share what I did.
I bought 50- to 70-year-old implements for a total of $2,625. Some were sold “as-is” with visible repairs needed. I also got a “pop-up” hay loader not counted in that figure. (I didn’t even know what it was until watching a video on YouTube.) This is likely the greatest invention since Noah parked the ark.
The high end on necessary horsepower estimates for the tractor come from the assumption that the hay will be mowed with a disc mower and baled with a round baler. The disc mower is very heavy and rides far to the right of the tractor, so weight is also a big factor to consider so the mower doesn’t tip the tractor.
I found that tractor size required was far less for an old sickle-bar mower. Imagine a 7-foot long set of barber’s trimmers. I now also know that I like this style of mower better than the new disc mowers for rough areas and uneven terrain.
A sickle-bar mower will slide over things that a disc mower will hit, possibly resulting in damage. This style mower is much lighter, so its effect hanging off the right side of the tractor is minimal.
I bought mine for $500, easily found an original manual online, and replaced and adjusted several parts to bring me from total ignorance to mowing hay in a relatively short time.
The total cost was $720. I have seen them online in various conditions for prices ranging from $200 to $3,000.
The man I bought my mower from recommended a Rolabar-style rake over the more common V-rake. Although any vehicle may pull rakes, a V-rake may require tractor hydraulics to raise and lower the two sides. This isn’t necessary with a Rolabar-style—the user can literally pull it with anything.
Mine was sold as-is and did require some missing parts and new tires. The total cost was $850.
The square baler was the long pole in the proverbial tent. I had seen our partner’s balers break or fall out of adjustment time after time. I was scared of losing several thousand dollars in pursuit of haying capabilities.
I found an ad on Facebook Marketplace by a gentleman in Missouri who has worked on balers for several decades. I drove 8 hours one way to buy a baler so old the bearing system for the plunger consists of four pieces of wood sliding in channels of angle iron. He had welded on a few niceties based on what he knew people found useful on a baler and had the knotter in tip-top shape.
For my first cutting, I counted close to 30 medium-to-major repairs I had to accomplish on these implements before I finished. Five were serious enough to involve welding. A few were catastrophic enough you would only expect one such failure per season of work.
However, I eventually got the hay baled and put up, and the knotter—the scariest and hardest part of a square baler to get working—worked like a champ.
In sum, although new implements could easily cost $45 to $50,000 and require 60 horsepower or more, I got everything I needed, made necessary repairs and covered my operating expenses for one cutting for about $3,800. And, perhaps more importantly, I was able to use my 48-horsepower tractor.
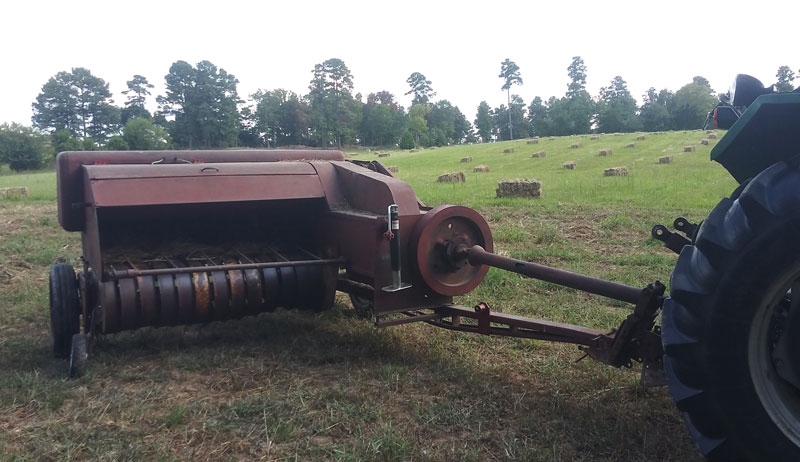
What Were My Results?
There were unexpected positive results to making our own hay. One was number of bales. People in the business of making hay as your partners are on the clock. They often fail to cut thoroughly, fail to rake to all edges and have no profit-incentive to stop and rebale a broken bale for that $2.50, e.g.
We went from less than 600 bales on our first cutting this year using a partner (for which we made less than $2,000), to 1,405 bales on my first solo baling experience.
Baling our own fields allowed me to optimize when each portion was ideal, when the weather was cooperative, when barn space was available, and when customers and bale-shaggers were ready. I watched my bales closely and reduced the number of “banana” and broken bales. My bales were the tightest and squarest we have ever put up.
Of course, operating costs and time are things each small farmer would have to consider when deciding whether equipment ownership and haymaking are the right answer. In my case, I made considerably more than my capital investment in one cutting.
Read more: When equipment fails, you can always gather hay by hand!
Hay Takeaways
My advice is to start with a partner who will let you do some of the work. You’ll learn the implements, the lay of the land and what it means when haymaking, methods and tips, and whether you enjoy it — all on someone else’s dollar. You can learn about pros and cons of different implement options. For example, when I mowed using our partner’s disc mower, all four drive belts fragged for some reason.
The cost to replace just those belts was nearly as much as my whole sickle-bar mower.
Buy equipment from people who use that exact type of equipment. The guy from whom I bought my cutter still uses a sickle-bar mower. He uses it on about five times the acreage I do. He could tell me exactly the optimal condition of grass to cut and the speed to drive, as well as problems to expect and how to avoid them.
He also drove an hour each way and helped me adjust my mower and learn to use it when I was at my wits’ end.
I bought the baler from a man who sold and maintained square balers for decades. He gave solutions over the phone for the repairs I needed to make and offered to drive six hours one way to help fix it on at least two occasions.
Old equipment is often easier to maintain and repair than new equipment. With new equipment the manufacturer may have engineered methods to keep the owner from being able to make repairs. Parts may not be available or they may come from a factory in remote parts of Asia.
With old equipment, repairing the old broken part may be a more likely option than finding a new one.
Many manufacturer-advised adjustments involve a hammer as the precision tool of choice. You can fix almost anything with a welder and a grinder. Don’t worry if you aren’t a very good welder. You soon will be.
It often doesn’t have to be perfect to work. Since the hay season of 2021, I’ve learned a couple of things. Back when the fields needed to be cut and baled, I knew my baler and my rake were missing a few pick-up tine. And I knew those wood-bearing surfaces were deteriorated in the baler. But I just pressed on and hoped for the best.
This winter, I replaced the broken tines and the wood bearings. They should be in tip-top shape to make hay in the summer!
The situation is different for everyone. But in our case, buying old haymaking equipment and making our own hay has been a profitable experience, financially and educationally.
Don’t let implement costs or single-source, biased information keep you from realizing this potential profit source for your small farm. If there’s a will, there’s a way.
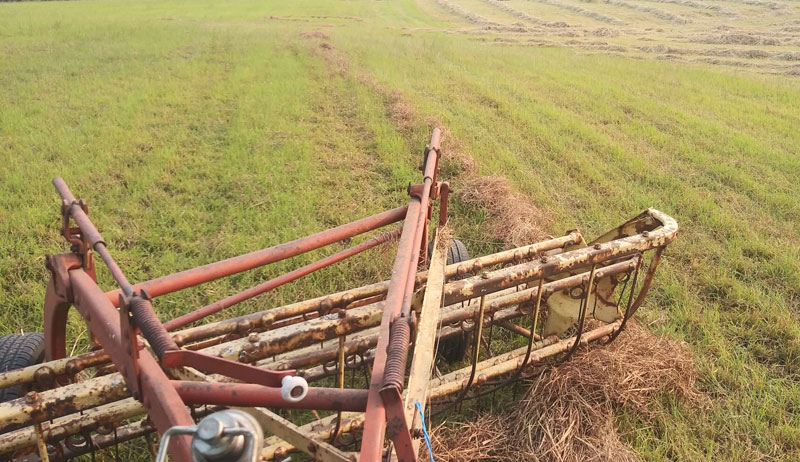
More Information
Improving Pastures
As the output of hay for the pastures dropped each cutting, and the desire was to provide better hay, we researched fertilizing the fields. We were intending to maintain a fairly natural, organic market garden on the property, so chemical fertilizers were off the table. Chicken litter was going to cost about $3,000 per application, which is unacceptable for a hay operation bringing us $2,500.
Then I began to learn more about the benefits of rotational grazing. I imagined that if I had extra plots to rotate through, the extras could be cut for hay and including these in the rotation would allow me to gradually improve all the pastureland. Because these would be smaller plots the hay operations would be very small each time.
I began to look for micro hay equipment. I found out two things: first, micro hay equipment comes with a macro price tag, often worse than traditional hay equipment. Second, the original hay partners had oversold me. My tractor was easily sufficient for running traditional hay implements.
This article originally appeared in the July/August 2022 issue of Hobby Farms magazine.