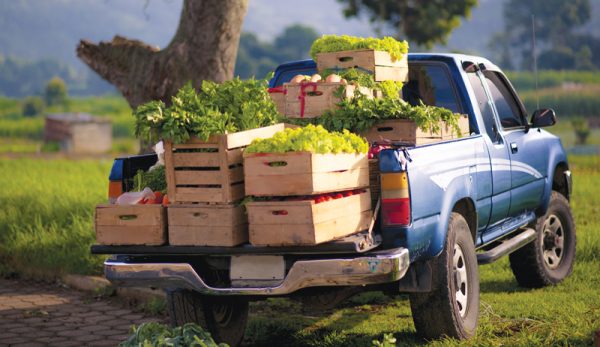
Regardless of whether it’s a wheelbarrow or a 10-ton tractor, it won’t roll when a tire goes flat. Let’s look at some ideas on tire inspection, tire sealants, inner tubes, leaks, repair and basic tire-maintenance equipment.
Tube or Tubeless
Tires continue on their long evolution from hard, solid leather bands around wheels to pneumatic tubes designed to cushion the sharp blows from rocks, potholes and bumps that cause vehicles to shake, rattle and roll. They are the interface between a vehicle and the road.
As such, they take quite a beating.
In the early days, rubber tires were unreliable, at best. And every automobile tool kit contained equipment to remove a tire from the rim and patch the inner tube.
Embedding steel cords in the rim of each tire made it possible to seal the tire against the rim. This eliminated the need for an inner tube.
Use of synthetics has greatly improved the lifespan and reliability of tires to the point where many commuters have never known the trials and tribulations of changing a flat tire on the shoulder of an interstate highway with trucks whizzing past just a few feet away at 70 mph. Improvements in materials and manufacturing have given us tires so reliable that they’re easy to overlook as part of routine maintenance.
Let’s start with what tires have in common, then look at some of the special requirements of the tires you have on the farm.
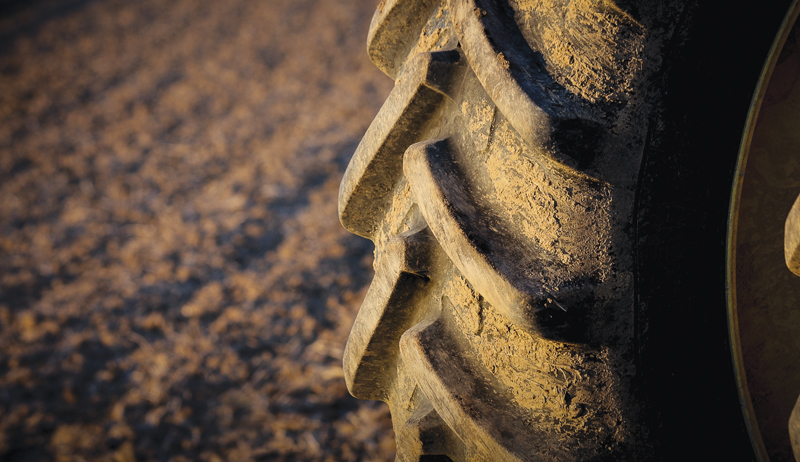
Tread on Me
Tread helps keep your vehicle moving—and stopping—in the desired direction. Intuitively, it might seem like the more tire that touches the road, the more traction you get. But unless you’re running on a drag strip, a bald tire can be quite dangerous.
The tread on a passenger car is designed to channel water to avoid hydroplaning (where the tire rides on the surface of the water, resulting in loss of control) and provide some grip on snow or shallow mud. A four-wheel-drive pickup, on the other hand, is less about comfort and more about getting there. The deep tread gives the most possible traction in snow and mud while providing suitable highway performance.
The general rule is to put a penny into the tread. If you can see the top of Lincoln’s head (about 1/16th-inch deep), it’s time to consider new tires.
The tread also tells you things about your vehicle. For example, if there is more wear on one edge of the tire than the other, the vehicle probably needs a front-end alignment. If there is more wear on both edges of the tire, you’re probably running it with less than the optimum air pressure.
This generates more wear on the tire and increases fuel consumption. More wear on the center of the tire indicates too much pressure.
Read more: Are radial or bias tires best for farm equipment?
Plies
One term that causes some confusion is the number of plies. Tires are manufactured in layers in which fibers run in different directions—much like plywood—for strength and flexibility.
More layers mean stronger tires capable of handling more pressure and heavier loads but also add expense.
For example, my passenger car has six-ply tires rated for a maximum pressure of 35 pounds per square inch, while my 3/4-ton, four-wheel-drive truck has 10-ply tires, and my 10,000-pound-capacity trailer has tandem 12-ply tires that inflate to 50 psi.
Under Pressure
Most tires have a maximum pressure listed on the side, and a vehicle’s manual provides a range of pressures. Keeping the tire at the minimum recommended pressure provides a bit more traction on snow and mud.
Running at the maximum pressure gives a rougher ride but improves fuel mileage. I run tires at the maximum pressure for this reason.
It’s easy to miss seeing a low tire on trucks and trailers with dual or tandem wheels, so take the time to check their pressure, too. At the very least, thump them with a bat or tire iron. If any have a lower pitch or produce a “flat” thud, check the pressure, and inflate or repair if necessary.
To get the maximum use from your tires, rotate them as indicated in the owner’s manual. That way, any uneven wear is distributed, and all tires will be ready for replacement at the same time.
Dealing with Leaks
Air has the irritating habit of trying to escape high pressure inside the tire. Keeping it where it belongs can be a challenge. As a general rule, if I can drive a vehicle to the repair shop before a tire goes flat, I do it, because a mechanic can remove the tire, repair it and replace it in less time than it takes me to find a lug wrench.
Of course, this might not be possible with a big tractor tire. To be safe and save time, take the tractor to a shop equipped to handle large tractor tires or have a mobile repair unit visit your place, which isn’t cheap.
Sometimes a slow leak can actually fix itself. If the valve is not seated, after airing up the tire several times, it might seal properly. The easiest way to test for this is a bit of saliva—or soapy water, if you prefer—on the valve. If bubbles form, you’ve found the problem, and you can probably fix it by pressing on the valve stem a couple of times to re-seat it.
After a while, it should become habit to give the valve the “spit test” every time you air up a tire.
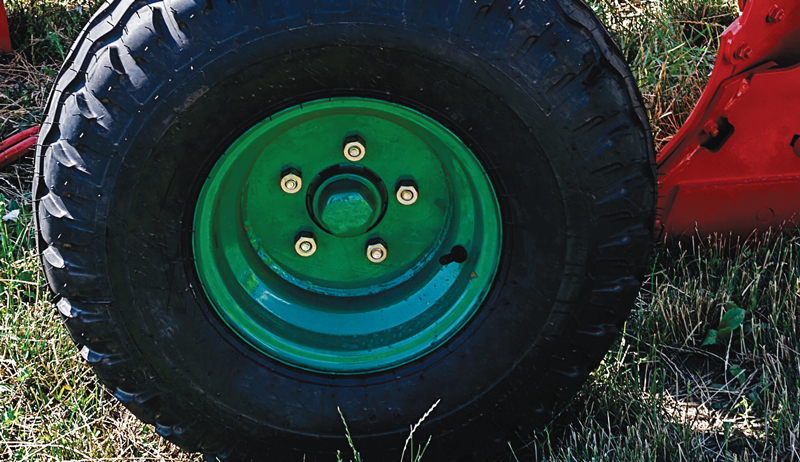
Next Steps
The next step in diagnosing a slow leak is to inflate the tire to the maximum pressure and spray soapy water on it. Look carefully for bubbles caused by air emerging from a leak. If you see none, move the vehicle or tractor to rotate the tire halfway and try again.
A nail can also cause a slow leak. In fact, it’s possible for the tire to seal around the nail tight enough that you don’t even detect it. If a tubeless tire has a nail or small puncture, use a kit—available in farm-supply stores—to plug it while the tire is still on the vehicle. This is an especially attractive option for tractor tires, as long as they are not liquid-filled.
The third common cause is separation of a tubeless tire from the rim, as can happen when you hit
a pothole. Again, soapy water is a good way to check for this. If the rim isn’t bent, a tire repair shop can fix it.
A bent rim on a highway vehicle means replacing the wheel. But you can save yourself some money on a tractor wheel by putting in an inner tube. It doesn’t rely on a tight seal between the tire and rim to hold air.
If you aren’t certain whether your tractor tire contains a tube, deflate it (if it isn’t already flat) and push on the valve housing. If you can push it in, there is a tube. Be careful not to push the valve stem all the way into the wheel, or you might have to remove the tire to retrieve it.
Read more: Check out these 4 creative uses for old tires around the farm.
“Off-Road” Vehicles
For nonhighway tires (on wheelbarrows, garden tractors, log splitters and low-speed trailers) filling a tire with foam can work. Because it doesn’t require the tire itself to hold air pressure, it’s a permanent fix. Some liquid sealants are also available.
Before resorting to them, be sure the leak is on the tread of the tire and not on the side, in the valve or between the tire and rim. These aren’t recommended for tires that run at highway speed. Also, once you use them, other repairs to the tire are impossible because patches will not stick.
Finally, tires on vehicles you don’t use often might have plenty of tread but be cracked to the point where they could go flat at any time—especially if you hit a pothole or road debris while hauling a load.
Before you haul your tractor to the tire shop, make sure your trailer tires are up to the task. A blowout on a trailer hauling a tractor that has a flat tire would be more than a double whammy. It would be downright dangerous.
This article originally appeared in the May/June 2019 issue of Hobby Farms magazine.