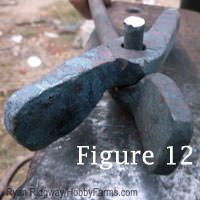
![]() |
No blacksmith shop is complete without multiple sets of tongs to hold hot pieces of metal. While you can sometimes find them for a reasonable price at auctions and antique stores, making your own tongs is a great way to practice all the techniques of blacksmithing:
- fullering to isolate sections of metal
- drawing the metal out
- rounding, punching and drifting the rivet hole
- upsetting to make a rivet
- welding on the tong reins
Before we begin, envision an A on your anvil. These three lines are the three steps in forging a set of tong bits to hold flat metal.
Materials You Need:
- 3/4-inch round or square steel for the tong bits (Approximately 2 to 3 feet is a good starting length to let you hold the metal with your hands, as you likely don’t have tongs yet and might need to draw the handles out rather than welding on a smaller rod. If you already have tongs for holding the rod, 3 to 4 inches is enough.)
- 1/2-inch round rod for the handles (Good rein lengths are 14 to 16 inches for using with coal or charcoal forges; 28- to 32-inch total length is required to make both reins.)
- hammer, anvil, forge and vise
- round punch and chisel or cut-off for your anvil hardy
- 1/4-inch to 3/8-inch rod for a rivet
- laundry borax for welding flux
- wire hand brush
![]() | Step 1: Forge the Jaw Begin by setting the end on the near side of the anvil to just under half its original dimension. Let the metal spread, as this will become a jaw of the tong. |
![]() | Step 2: Forge the Rivet Boss |
Many people don’t realize that there are left- and right-handed tongs. To make them comfortable, always rotate the metal away from your body, regardless of which hand you use. Because I’m left-handed and hold my tongs in my right hand, I rotate the metal clockwise. If you use your left hand to hold your tongs, rotate the rod counter-clockwise. When the tongs are finished, this puts the reins in the proper orientation to keep them from rolling out of your hand. |
Step 3: Forge the Rein Attachment Isolate the rivet boss, and begin forging the rein over the far side of the anvil. If using a 1/2-inch rod for the reins, draw the rein end out until it’s approximately 5/8 inch wide. You always want to have extra metal available when forge welding to allow for refinement of the weld. | |
![]() | Figure 4 shows the finished tong jaw before cutting it from the parent metal.Prepare the jaw for welding by creating a bevel and thin edge, known as a scarf, as seen in Figure 5. |
![]() | To prevent breaking at the handle, the scarf should be along one side of the jaw, as shown, not top to bottom, as this gives the most surface area for the weld to hold when the tongs are squeezed. If the scarf is made top to bottom, rather than along a side, the weld can peel apart when the handles are squeezed. If you don’t have a welder or a second set of tongs to hold the finished jaw, don’t cut it off of the parent material; simply forge the handles out. |
Step 4: Punch and Drift the Rivet Hole To make your jaws as symmetrical as possible, make the second jaw while your measurements are fresh in your head. Use your first jaw as a template and ensure they freely open and close on the rod you’re using for the rivet before riveting. |
![]() |
Step 5: Welding the Rein |
![]() | For your first set of tongs, if you haven’t practiced forge welding and you have a different welder, tack the rein to the jaw bit but don’t fully weld them together. This will allow you to practice welding without the stress of having to line up pieces. If you don’t have a welder, have a helper hold one piece for you. |
![]() | You will need to clean your fire of any clinker that might have developed and build a deep nest of charcoal, or coke if using coal. It needs to be deep enough to use the oxygen in the air from your blower as oxygen can alter the metal and prevent the forge weld. To reach forge-welding temperature, the center of the fire needs to be bright yellow, almost white, and when your metal is hot enough, it should appear like hot butter and be difficult to see in your fire. |
To forge weld, heat the metal until it is orange and clean the scale off with a wire hand brush. This scale is oxidized metal and doesn’t weld properly. After cleaning the weld area, apply a liberal amount of borax until covered. Return the piece to the fire, and take it up to welding heat. Once it’s at welding heat, work fast before it cools. Lightly but solidly hammer the weld together, increasing the strength of your stroke as it begins to feel more solid. Only hit the metal at 90-degree intervals to prevent shearing the weld. If your metal isn’t the color of melted butter when it cools, wire brush the weld, re-flux it and heat it back up. |
![]() | Once the weld is solid, it’s time to round the reins (Fig. 9) where you had forged them square. Begin by holding the metal so that two corners are perpendicular to the anvil, and forge them into the center. Repeat this step on the other two corners to create an octagon. Continue forging the corners into the center until it becomes round and there’s a smooth tapering from the rivet boss to the rein handle with no thin points to break. |
![]() | Step 6: Forge the Rivet Heat the end of the ¼-inch rod to a bright yellow. Using your vise, begin to forge the end back into the rod (Fig. 10). To prevent it from bending over, keep only half the rod diameter above the vise and alternate the sides that you are striking it from. |
![]() | Once you have one head on the rivet, slide the tong halves onto the rod and mark the length you need for the other rivet head. For most rivet heads, you’ll need up to twice times the diameter of the rivet. Partially cut the rod at that mark (Fig. 11) and heat rivet, still on the rod, to a bright yellow. Break the rivet off the rod, and assemble the tongs quickly. |
![]() | Once assembled and on the anvil face (Fig. 12), solidly hit the rod straight down to upset the rivet head. Rotate the tongs as you forge the head to prevent it from bending over. |
Once you have assembled the tongs, it helps organize your tong rack if you create a space between the reins by closing them with a rod the size of your tong rack behind the boss. Now you can adjust the rivet tightness so that they open and close easily but don’t wobble.