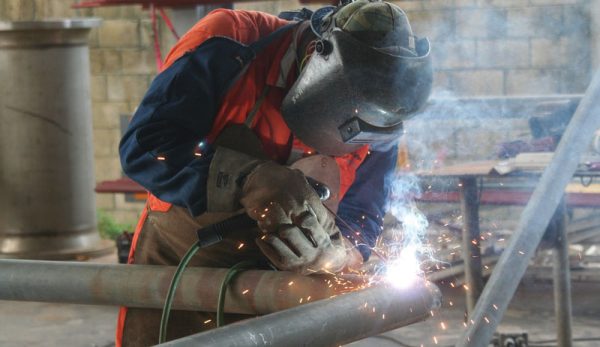
Picking up a cheap welder can save you a lot of money. You can quickly repair gates, fences and machinery without hiring someone to do it or allowing it to get more damaged.
The most common welding method used on farms is stick welding. It offers a few key advantages such as cost and portability.
However, stick welding isn’t right for everyone. And some farmers prefer to use a wire welding process such as metal inert gas welding or flux-cored arc welding.
Stick Welding
Stick welding (shielded metal arc welding, aka SMAW) is one of the most popular welding processes. It’s a simple procedure that is popular with outdoor welders due to it not being affected by wind. (For a stick welding how-to, check out this link.)
SMAW Pros
- Easier setup. It’s simple to set up, and you don’t need to connect a gas cylinder.
- Portability. Stick machines can be very light and portable. They’re easy to carry around.
- Suitable for windy conditions. Stick doesn’t require shielding gas. Welding processes that use shielding gas won’t get good results in windy conditions because the wind will interfere with the gas.
- Cheaper. Stick machines are some of the cheapest welders on the market
- Rusty metal. Metal doesn’t need to be clean before stick welding. So it’s good if your metal has bits of rust or paint that you don’t want to clean off.
SMAW Cons
- Unable to weld thin metal. Stick welding is very hot and isn’t suitable for welding 18-guage sheet metal.
- Cleanup time. SMAW doesn’t produce clean welds, and there is a lot of spatter. If you want to reduce cleanup time, stick isn’t for you.
- Skill level required. Stick is a harder process to learn, as you need to learn to strike the arc.
- Slow process. Stick welding is slower because rods need to be changed. Wire welding, however, uses a continuous spool of wire.
SMAW Farm Tips
- Wet or damp electrodes make it more difficult to lay a strong weld. Store electrodes in a cool dry place.
- Don’t hold the rod at 90 degrees to the metal. For best results hold it at approximately 75 degrees.
- Don’t hold the electrode too far away from the metal. Arc length should not be greater than the diameter of the electrode.
- Moving the electrode too slowly can cause too much metal to be deposited and a weaker weld with a convex bead. Similarly, a fast travel speed will create a narrow concave bead with low penetration.
Read more: Should you learn welding for farm repairs? Yes! Here’s why.
Metal Inert Gas Welding
Metal Inert Gas (MIG) welding (also known as GMAW) is a really popular type of welding that’s frequently used for welding low-alloy steels. It is well suited for welding auto-body parts and home-
repair projects.
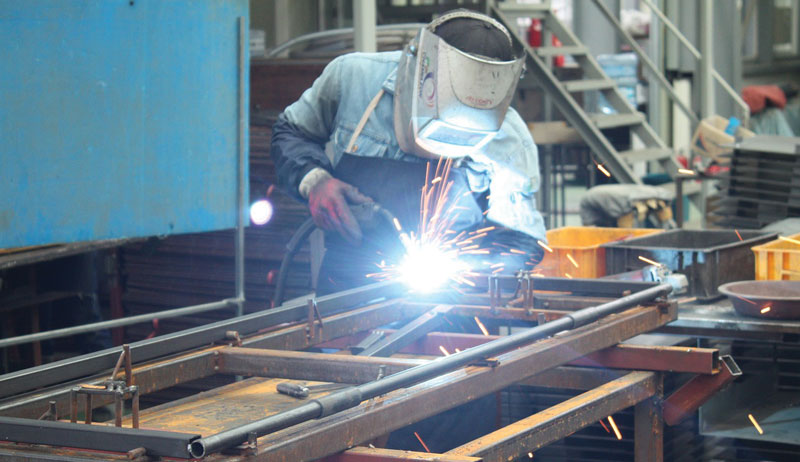
MIG Pros
- Better quality welds. MIG welds produce less spatter so cleanup time is reduced.
- Suitable for thinner metals. MIG is versatile and will easily weld 18-gauge steel.
- Continuous process. You don’t need to change rods like you do with stick. You use a wire spool so you can weld near continuously.
- Easier process. MIG is easier and more reliable. Once you’ve set up the welder, you basically need to hold the gun at a certain distance from the metal and press the trigger.
MIG Cons
- More expensive setup. MIG welders are typically more expensive. Plus, you need a gas cylinder as well, which can add up.
- Not suitable for windy conditions. MIG requires shielding gas to protect the weld from contamination. In windy conditions, the wind can interfere with the gas and cause the weld to be contaminated.
- Not portable. MIG welders are typically heavier than inverter stick welders. You’ll need to transport a gas cylinder as well.
- Need to clean metal before welding. If you have metal that has rust or paint on it, you’ll need to clean this off before you can use MIG.
MIG Farm Tips
- Listen to the sound the arc is making. If you hear a sound like you’re frying bacon, then you’re doing it right. If it hisses, then your voltage might be too high. And if it’s loud and crackly, it might need turning up.
- The stickout is the length the wire sticks out from the MIG gun. Keep this short at around 1⁄4 inch for a more stable arc.
- In MIG welding, you only need to use one hand to hold the gun. Use your second hand to steady and support your hand holding the gun for extra precision and comfort.
- Have the arc positioned at the front of the weld when pushing forward. This will help for better penetration.
Read more: You can build your own farm tools with basic welding skills.
Flux-Cored Arc Welding
Flux-cored arc welding (FCAW) and MIG welding can both typically be performed with a standard MIG machine. The key difference: MIG requires use of a gas bottle; FCAW doesn’t.
FCAW Pros
- Continuous process. FCAW uses a spool of flux wire so you don’t need to stop and change rods.
- Portable. FCAW doesn’t require shielding gas because the wire contains a flux which protects the weld from contamination. You don’t need a gas cylinder.
- Can be used in windy conditions. The lack of shielding gas means FCAW can be performed in windy conditions without threat of interference.
- Basic operation. Similar to MIG, FCAW is a basic process and even easier than MIG because you don’t need to connect a gas cylinder.
- Rusty metal. FCAW is forgiving on metal that has rust or isn’t clean.
FCAW Cons
- Produces lots of fumes. Smoke and fumes are released from the flux coating. So you’ll need to be in a well-ventilated area, ideally wearing a respirator.
- Requires cleanup. In addition to fumes, high amounts of spatter are released.
- Not suitable for aluminum
- Not suitable for thinner metals. The thicker wire and higher temperature makes FCAW unsuitable for welding thin-gauge steel.
- More expensive wire. FCAW has a cheaper start-up cost than MIG. However, wire is more expensive and can add up overtime.
FCAW Farm Tips
- MIG uses DC electrode position (DCEP), but FCAW uses DC electrode negative (DCEN). Make sure you have the right settings.
- Flux cored wire is softer than MIG wire and is more likely to get tangled or birdnested. To avoid birdnesting, use knurled V-drive rollers.
- If the tip of the electrode touches the weld pool, it can fuse the hollow wire shut and break a good weld. Keep the tip away from the metal.
Hopefully these tips help you choose the right welding process for you and get you even better results on the farm. Check out this link for more advice on choosing a welder.