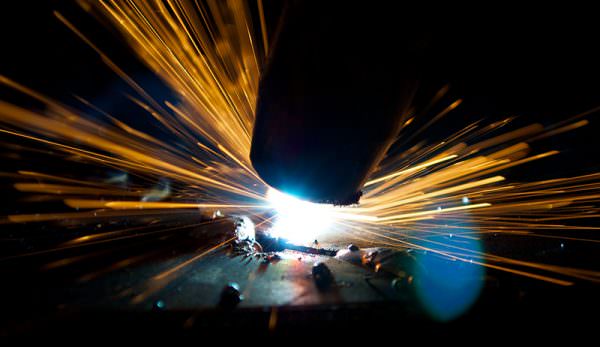
Hobby farming is never boring. From examining strange livestock noises in the middle of the night to the never-ending battle against pests, there are rarely dull days in the world of agriculture, no matter how small your operation might be. Unfortunately, that excitement isn’t always a positive thing. Occasionally, it can stem from broken materials and equipment around the farm, forcing you to get a little creative to avoid shelling out hundreds or thousands of dollars for repairs. Enter one of the farmer’s most useful repair tricks of the trade: welding.
From quick fixes for fences and gates to intensive tractor and farm-machinery repair, having a welder on-farm (and the required knowledge to safely use one) could mean the difference between purchasing a brand-new piece of machinery and quickly and efficiently restoring broken parts to proper working order.
That said, choosing the right welder for you and your farm is not necessarily a straightforward, simple process—there are a variety of welders on the market, and not every welder is cut out for every repair job. Here’s a breakdown of various welder specifications, from process and currents to duty cycles and amperage outputs.
Welding 101
There are three major types of welding processes: stick welding, metal inert gas welding and tungsten inert gas welding, each with individual pros and cons. (There are additional welding processes, including flux-cored arc welding and plasma arc cutting, but hobby farmers will most commonly come across these three major types.)
Stick Welding
Also known as arc welding, stick welding is the most popular method for noncommercial uses, due mainly to its affordability and the equipment’s portability. These welders strike an electric current, or arc, between the welding electrode, aka stick—you can see where the machinery and process get their names—and the base metal, which in turn melts the electrode and creates the weld.
Because the electrode is constantly being melted, these welding machines require frequent stick changing, which also makes them somewhat difficult to use. Striking and maintaining an arc requires considerable skill: Pulling back too far on the welder after striking the electrode will break the arc. A successful weld might also take multiple electrodes to repair, and stick welders tend to melt through base metals thinner than 1/8 inch.
However, the pros of stick welders will likely outweigh the cons in the long run. They’re far and away the most economical welders on the market, and you can use them even in windy or rainy conditions, not to mention on dirty or rusty metals—huge boons for farmers and ranchers.
MIG welding
Unlike stick welding, MIG welding is a semi-automatic process. An arc is created between a spool of electrically charged wire and the base metal, which melts the wire and creates the weld; the wire is automatically fed into the weld at a preselected speed, allowing for longer, cleaner welds. Because the arc doesn’t need to be restruck, MIG welders, such as the Millermatic 211 from Miller Electric, are significantly easier to use than stick welders and can also be successfully used on thinner metals.
Regardless, MIG welders cost considerably more upfront, and the machinery is more complex and less portable than stick welders, potentially restricting their on-farm usability. Additionally, they work best on clean base metals, so all dirt, rust and paint must be scraped off prior to use.
Tig Welding
This type of welding is similar to MIG welding, with a few major differences. Instead of using a metal electrode, TIG welders use a non-consumable tungsten electrode to strike and maintain the arc and produce a weld. Because the electrode is not consumed, filler metal is required to form the weld, and a shielding gas is also needed to protect the weld from the environment as it is being created—stick electrodes are coated in a metal that automatically creates this shielding gas as the electrode melts.
TIG welders are quite expensive and require the highest skill level to operate, though they offer the most precise and high-quality welds available. They also create the most aesthetically pleasing welds of the three major types, making them ideal for metalworkers who make decorative or functional pieces for display.
Types Of Currents
All welders require a power source to run—either electricity or gas—and they can also differ in how they harness that power source and transform it into an electric current. Because currents each have a negative pole and a positive pole, the flow of electrons between the poles creates three major current types, each with specific benefits and drawbacks. Welders are clearly labeled with their current type, sometimes even in the model name itself, and many on the market can toggle between the currents with the flick of a switch.
Direct Current
This current flows in one steady direction, which results in a constant electrical polarity. Direct current welding enables welders to start arcs more easily, as well as maintain a smoother arc during the weld.This current type can be broken down further, depending on the direction of the electron flow.
- Straight Polarity: More accurately termed electrode-negative polarity, this current type works best on thinner metals at the expense of faster electrode burn-off.
- Reverse Polarity: Also called electrode-positive polarity, this current type is best for thicker metals, as it results in deeper penetration of the base metal.
Alternating Current
Like the name suggests, this current alternates direction, flowing one direction half the time and a different direction the other half. Because of this, it can be slightly less predictable than a DC welder, but its major advantage is that it can successfully weld metal that has become magnetized through friction. Alternating current welders, such as the Lincoln Electric AC 225 Arc Welder above, are subsequently more versatile across the farm, as the frequent rubbing of hay, feed or water can magnetize some metals, including steel.
Duty Cycle
Duty cycle is another important specification to take into account when looking for a welder. The term refers to the percentage of a 10-minute cycle that a welder can operate without overheating. A welder with a duty cycle of 50 percent can operate for five minutes before it needs to rest and cool for five minutes. Duty-cycle measurements are also directly related to a welder’s amperage output: A welder might have a 20-percent duty cycle at high amperages, but a 100-percent duty cycle at lower amperage outputs. Most welders on the market allow for adjustable amp outputs, which change based on the thickness of the base metal you’re working with—the thinner the material, the lower the amp output should be.
As you peruse the market offerings, keep in mind the welder is not your only purchase: You’ll also need to buy safety equipment, including a helmet, jacket and gloves, as well as shielding gas and electrodes if necessary. If your budget and welding needs are limited, consider renting a welder from your local equipment shop or welding manufacturer for on-farm repairs, giving you the convenience of welding for a fraction of the overall cost. Before operating any equipment, either purchased or rented, thoroughly read the manual, as improper use can lead to eye injuries and high-level burns. Additionally, practice your welds on scrap metal before trying them on the base metal in question to familiarize yourself with the process and the welder’s controls.
With a little research and practice, you’ll be fixing gates and doing metalwork in no time at all, keeping your life exciting in all the best ways.
This article originally ran in the November/December 2013 issue of Hobby Farms.