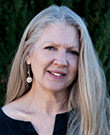
I haven’t made paper in several years and decided it was time to give it another try. When I first started papermaking, I made it from recycled paper, but later moved to making 100-percent cotton rag paper from cotton linters. Cotton paper is beautiful and strong, with options for natural dying and for inclusions like dried flowers, pressed leaves or shiny oat straws. Last summer, I was dying some fabrics and yarn with indigo I grew, and the linters were sitting there, tempting me to throw them into the vat. Why not? It turned a beautiful blue as I squeezed out the liquid and let it oxidize on a strainer. It sat in the strainer in the garage for many months, and now I have beautiful blue paper!
According to the Robert C. Williams Museum of Papermaking at Georgia Tech, paper was first made around 100 B.C. in China. Early Chinese paper was made with hemp, beaten with a wooden mallet and made with a coarse sieve. The primitive paper I produced was beaten in an old kitchen blender, and the mold was made of old picture frames with dime-store tulle stretched across and stapled to the edges. Another improvement made by the Chinese was the use of starch as a sizing material; I used gelatin water.
As papermaking moved into Korea the pulp expanded to include rattan, mulberry, bamboo, rice straw and seaweed. It took almost 500 years for papermaking to reach Europe. Techniques improved over time, and different regions began using their native fibrous plant.. Paper can be made out of most any cellulose fiber or combination of fibers. I can’t wait to experiment with the plants in my yard, once the snow and deep freeze is a memory. For now, I’m using the tough greens of leeks from the grocery store, cotton linters from Earth Guild and some recycled packing paper.
If you’d like to try your hand at homemade paper, follow the directions below.
Tools
- old kitchen blender (used only for crafting)
- old picture frames or craft frames, sized for a sheet of paper
- tulle or fine net
- scraps of pellon (sewing interfacing; optional)
- heavy-duty stapler
- large plastic tub
- scissors
- needle
- thread
- couching cloths (squares of old heavy fabric or felt): I used my grandma’s old curtains cut into 20-inch squares
- sponge or towels
- flower press
Paper Materials
- 4 cups fibrous plant material (leeks, iris, yucca, hostas, grasses, hemp, linen), recycled paper with minimal printing and prepared cotton linters https://www.earthguild.com/products/papermak/lintpulp/pappulps.htm
- water
- unflavored gelatin
- dried flowers or leaves (optional, for texture and design)
Step 1: Make the Molds
Cut the tool or fine netting 3 inches larger than the frame you’ll be using as your paper mold. Stretch and staple the net to the frame, wrapping it over the edges.
If you want to make special shapes, cut them from pellon and sew the outside section to the stretched screen, close to the edges. I used a heart shape.
Step 2: Cook the Fiber
Cut the plant material into 1/4- to 1-inch sections with strong kitchen scissors or a knife. (You should get about 4 cups worth.) Place in a large pot with cotton linters and cover with water. Bring to a boil, lower the heat and simmer for an hour or two, depending on the toughness of the plant.
Drain the plant material through a piece of net, and squeeze out as much water as you can. Rinse it with fresh water, again, squeezing out as much water as you can until the water runs clear.
Spread out the fiber and dry it for later use, or proceed with the papermaking.
Step 3: Make the Pulp
Fill an old kitchen blender fill the jar three-quarters full of water. Add a small handful of fibrous material, and blend until it’s suspended—it could take as long as two or three minutes for the plant material and as short as 30 seconds for recycled paper. Make sure the fibers don’t wrap around the blade and burn out the motor. (Mine was smoking at one point—I caught it just in time.) Dump the blended pulp into a bucket, and continue processing the rest of the fiber material.
Dried flowers or leaves can be added during the blending process. You can choose to sprinkle them over the pulp in the tub or over the newly formed sheet of paper before it’s pressed (see step 5).
Step 4: Prepare Your Workspace
Select a table or counter space where you’ll be processing the paper. Lay down two to three sheets of couching fabric or a piece of thick blanket next to your large tub. Have a towel or sponge readily available for cleaning up spills.
Step 5: Make a Sheet of Paper
Fill your large tub with at least 3 inches of water. Add up to 4 cups of pulp to the tub, and stir with your hand to evenly distribute the pulp.
Hold the mold screen side up, with your hands on both sides. Dip it under the pulp and lift up with the screen perpendicular to the water to collect pulp on the screen. If the pulp isn’t even, dump it back into the vat and mix again with your hand. Hold the screen over the tub to let excess water drain. You can tilt it to let the water run off.
Carefully flip the screen over onto the couching cloth, using a steady movement so the paper doesn’t wrinkle. Use the towel or sponge on the back of the screen to collect excess water. Carefully lift up on one edge of the screen to release the paper onto the couching cloth. You may have to urge it to release with your fingertip or a flat utensil, such as a palette knife. Lay another couching cloth on top of the paper.
Repeat the process to make more sheets of paper, creating a stack of paper between couching cloths. You can generally do six to 10 sheets in one stack. Add more pulp to the tub if the sheets get too thin.
Once you’ve created a stack, place the entire stack in a flower press and secure the pressure. (If you don’t have a flower press, a board and weights will work.) Press the stack for 30 minutes to an hour. This will allow the fibers to settle and help them adhere to each other.
Hang up the couching cloths with the paper adhering to them to dry. I used clothespins on a drying rack. Let dry overnight.
Step 6: Size Your Paper
Sizing or size is a material added to your paper to reduce its tendency to absorb liquids once dry. It will prevent pen ink from bleeding, though it’s not necessary if you use ballpoint pens or acrylic paints.
For writing with ink, I used a gelatin size. (You can also use a clear gesso.) Dissolve 1/2 teaspoon of unflavored gelatin into 1 cup warm water. Brush with a soft brush over the surface of the paper while it’s still attached to the couching cloth. Hang up to dry.
Step 7: Press Your Paper (optional)
When the paper is dry, gently peel it off the cloth. The texture of the cloth will be impressed on the paper. If the paper is too wavy for your taste, press again under weight for a day or more until flat. You can also use a warm dry clothes iron.
Alternative Project: Silk Paper
I’m not sure this product actually qualifies as paper, but it can be fun to try.
Spread netting out on a smooth worktable and cover a 6-by-8-inch section with silk noil fiber, gently teasing it apart and distributing it fairly evenly. Covered with another sheet of netting—or fold the first piece over, creating a silk sandwich with net on each side.
Make a paste with 1 tablespoon cornstarch with 1 cup water, cooking until thick and clear; let it cool. Scoop up a handful of the paste, and work it into the silk-and-net sandwich. When one side is covered, flip it over and added more paste to areas that are still dry.
Carefully removed one side of the net and hang it to dry overnight. The following day, peel the other sheet of netting from the silk, and press the silk under weight for a day.
![]() | About Patricia Lehnhardt Patricia Lehnhardt is a shop owner, freelance writer, photographer, gardener and long-time crafter of all things natural from the Midwest. |