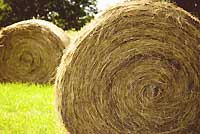
Make Your Own Hay Manufacturer Spotlight Massey New John Deere Hesston |
If you keep any sort of livestock, you probably feed baled hay.
Whether it’s cheaper to buy or bale your own depends on a slew of variables, including whether you have access to established hay ground, if you own haying equipment, and if you have the time and the physical wherewithal to do this heavy job yourself. However, you’ll invariably have more control over the finished product when you bale your own.
According to the National Agricultural Statistical Reporting Service, in 2002, American farmers harvested 151 million tons of hay. Nearly all of the hay produced in
Long before balers, country folk hayed with scythes and pitchforks, a time-consuming, backbreaking task that was lightened somewhat with the invention of the horse-drawn sickle mower and stacker, along with grappling hook apparatus designed to lift cured hay into overhead hay mows.
Stationary balers were introduced in the mid 1800s. Workers forked loose hay into one end of these horse-powered units, while others hand-tied compressed bales as they exited the other end.
In 1903, Ummo F. Leubben of
In 1940, Leubben sold his rights to Allis-Chalmers, who redeveloped his early concept and in 1947, released their own Roto-Baler.
Balers Beware Haying accidents can result in horrific injuries or death, so whichever baler you choose, always reduce unnecessary risk by conscientiously following these safety protocols.
|
Within three years, Allis-Chalmers marketed more than 23,000 Roto-Balers.
Top
Meanwhile, in 1936, a “man named Innes,” of
Building on this innovation, in 1937, Pennsylvanian Ed Nolt used knotters from the improved Innes baler to hand-build the first successful automatic pickup square baler. New
Farmers loved the 66; New Holland ultimately sold 84,000 of them. The New Holland 66 put up 14”- x 18”-bales, whereas the company’s larger New Holland 77 and competitors’ models spit out a heavier, bulkier 16”- x 18”-bundle—and with its wheels removed, the 66 was only four feet tall, making it more economical to ship. The New Holland 66 cost a mere $1,850 (the 77 model ran nearly $2,500). It was the forerunner of the neat, small balers we highlight here.
Like their predecessor, our comparison models process hay into easy-to-handle, stack and store 14”- x 18”-bales. All require 30 to 35 horsepower or larger tractors equipped with 540 rpm PTOs.
All can be fitted (at additional cost) with bale throwers, bale chute extensions, hydraulic pickup lifts and bale tensioners, and wagon hitch kits.
Most offer an optional quarter-turn bale chute that drops bales on their sides in the perfect position to be retrieved by automatic bale wagons. What differs is their basic design.
Agco Corp.
Two of our balers, the New Holland Model 565 and John Deere’s Model 328, are configured in the traditional manner: The baler operates offset to the right side of the tractor with the hay wagon trailing behind the baler. However, Massey Ferguson’s 1835 baler and Hesston’s Model 4550 are built in a straight-line design that moves hay in a straight path from the windrow to the bale chute, thus preserving nutritious leaves that might otherwise be lost in the baling process.
Each design has its advocates, but most agree straight-line balers are easier to maneuver through gates and around small fields.
Agco Corporation, the company that manufactures Massey Ferguson and Hesston machinery, says straight-line design reduces strain on its baler frames, too.
While each has unique features unto itself, the Massey Ferguson 1835 and Hesston 4550 balers share a slew of stellar attributes, among them
- Curved pickup teeth to nab hay other balers miss;
- Centering augers that reduce windrow size to accommodate 61” pickup assemblies;
- Dual-gauge pickup wheels to help reduce bounce and constant-velocity drive shafts.
Both incorporate a straight-line prepacker chamber that pre-forms each flake before sweeping it into the bale chamber, thus ensuring consistent bale density and uniform flake size.
New
The 565’s high-strength, long stroke, steel plunger runs on sealed ball-bearing rollers and white-iron slides for minimal maintenance and fewer adjustments while packing uniform, dense bales in all crop conditions. It boasts a category 3 driveline and New Holland’sexclusive Power-Pivot PTO.
John Deere
John Deere’s Model 328 is another high quality haying machine. It’s better features include 104 closely spaced pickup teeth and narrow-channel, flanged strippers that extend to the flare; a crank-raised pickup that permits infinite height adjustment within a 5” range; five-position, spring-loaded feeder forks to match feeding requirements to crop conditions; adjustable nine-position hay compressors; crank-adjustable top and bottom tensioners with t-rails to assure uniform tension; and John Deere’s unique, category 3, equal angle two-joint PTO.
About the Authors Based in Arkansas, John and Sue Weaver have been hobby farming and home buying for more than 20 years.
This column first appeared in the July/August 2005 issue of Hobby Farms magazine. Subscribe to Hobby Farms today!